HTW® Gasification
The High-Temperature Winkler (HTW®) technology is the most developed proven gasification technology utilizing waste-based feedstocks. The process was originally developed in the 1920s by the German energy company Industrie Gewerkschaft (IG). Over the years, the technology has been significantly improved to achieve better results and has been re-engineered to handle a broad range of feedstocks.
GIDARA Energy acquired the technology in 2019 and has further developed it to meet current technological and environmental standards.
History
HTW® gasification is one of the most developed proven gasification technology utilizing waste-based feedstocks. In the 1970s, Rheinbraun (now RWE) improved the process by operating the gasifier at a higher temperature to increase carbon conversion and improve syngas quality. Further development focused on increasing gas throughput, flexibility to operate with either air or oxygen and increased efficiency.
The repurposing of HTW® gasification towards bio-applications began in the 1980s and 1990s. Initially, the Berrenrath (Germany) unit tested various waste feedstocks and demonstrated stable operation. The Niihama (Japan) unit further demonstrated the viability of waste and bio-gasification.
In 2010, ThyssenKrupp Uhde acquired the HTW® technology from RWE and further developed it. The combined investment since 1970 exceeds 500 million euros.
In 2019, GIDARA Energy acquired the technology from ThyssenKrupp, further developing it for sustainable applications.
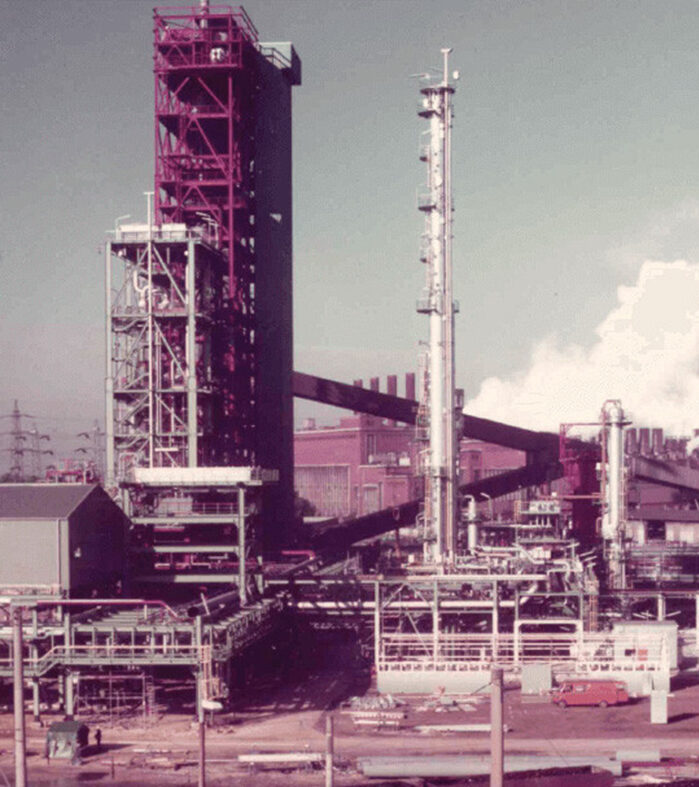
The HTW® gasifier is a bubbling fluidized-bed (BFB) reactor that operates in either air or oxygen-blown modes. It is a dry-feed, pressurized, dry-ash gasifier. A key advantage of the technology is the capability to gasify a variety of different feedstocks, including various forms of biomass, refuse-derived fuel (RDF), and municipal solid waste (MSW), which have all been commercially applied. All grades of more reactive low-rank coals with a higher ash softening temperature (i.e., brown coal) have been commercially applied.
Due to the high outlet temperature, the syngas does not contain any higher molecular weight hydrocarbons, such as tars, phenols, and other heavy aromatics.
In the fluidized bed, a high material and energy transfer rate is achieved and this guarantees a uniform distribution of the temperature throughout the gasifier. The temperature is maintained below the ash softening point.
Process description
The HTW® system mainly consists of a gasifier and a cyclone with a gravity return pipe, which is used for converting feedstock to syngas. Due to the pressure in the gasifier, both the feeding system, as well as the bottom ash and dust removal, have to be performed by lock-hopper systems. With the aid of the gasification agents, i.e. oxygen (O2) and steam (H2O), the biomass-derived material is converted in the gasifier to the raw syngas (CO & H2).
The major part of the carbon conversion takes place in the lower section of the gasifier where the feed particles are in a fluidized state. The fluidization gas consists mainly of the gasification agents and the raw syngas formed. In the so-called post-gasification zone, which is formed in the upper section of the gasifier, more oxygen and steam are added to complete the gasification process, improving the gas quality and the conversion rate due to the temperature increase. The majority of fine ash particulate and dust entrained in the obtained raw syngas are removed in a cyclone and returned to the gasifier for a higher conversion rate and raw syngas is cooled in a gas cooler by producing high-pressure steam. Ash is removed from the base of the gasifier through an ash discharge system and dust is removed in a dry dust filter.
Watch our video
An example of HTW® technology integration into a value chain is the production of methanol from non-recyclable waste. Learn about the process steps from waste to sustainable fuels in the video below.